【Vacuum pump】Vacuum pump Technical Service Solutions
Background of Customer
The cooperative customer is a special equipment manufacturing company specializing in the production of vacuum pumps and vacuum systems, focusing on serving the environmental protection industry. The customer's products are widely used in vacuum drying and dehydration, vacuum impregnation, vacuum metallurgy, vacuum coating, vacuum concentration and other fields. It is a professional manufacturer integrating development, production and operation of vacuum equipment.
The problems customer meet
In response to market demand, customers need to improve the performance of vacuum equipment, high speed, low noise, high efficiency, etc., and put forward higher requirements in terms of bearing load, speed and noise.
The original supporting bearing has been unable to meet its high-speed, high-load, low-noise high-demand operation requirements, resulting in the risk of frequent maintenance and increased use costs.
During the operation of the equipment, the extremely high load and rotational speed put forward more stringent requirements for the operation of the equipment. After the original equipment has been running for a period of time, the bearings, which are the main components of the vacuum pump, will suffer from rapid fatigue wear and increased friction. There is a high-decibel noise that bothers customers from time to time.
Having a bearing product that can adapt to higher speed, larger load and lower noise has become a product problem that customers need to solve urgently.
The solution providing by THB
Product Failure Analysis:
Analysis of the problem bearings used by customers, the following problems can be clearly seen:
1. (Because the inner hole of the inner ring and the shaft diameter are matched with a clearance fit, creeping occurs between the inner hole of the inner ring and the shaft during operation. From the photos, it can be seen that the surface of the inner hole of the inner ring has creeping corrosion, which will also cause abnormal temperature rise of the bearing.)
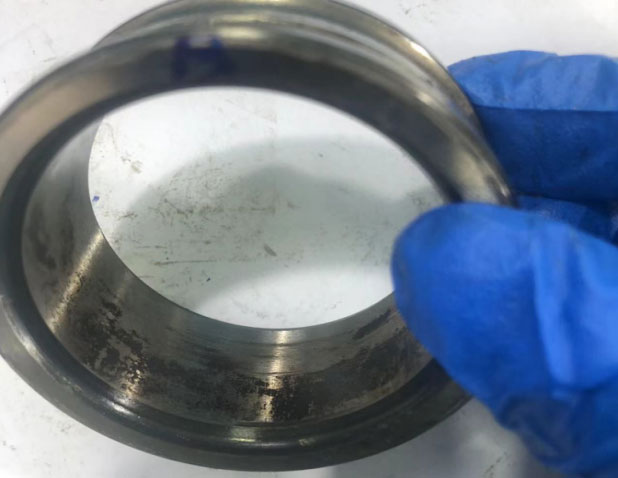
2. It can be seen from the photos that in the two rows of raceways, the contact fatigue area of one row of raceways basically covers the entire raceways profile, while the surface of the other row of raceways is only slightly worn radially. It shows that the axial clearance of the bearing is improperly selected, resulting in the two rows of raceways not being able to bear evenly during the working process. One row of raceways is subjected to both axial force and radial force (and there is a slight misalignment), while the other row is basically not subject to axial force, only radial force and radial force load is not large.)
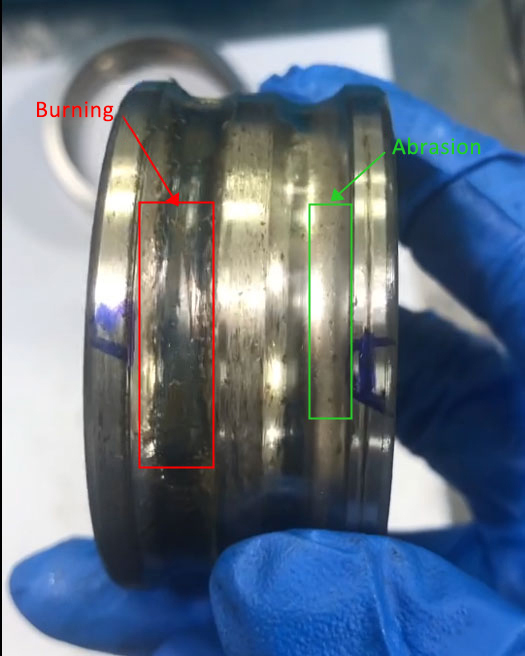
Product optimization:
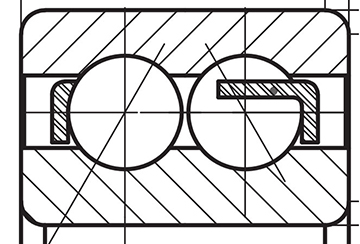
1. The aspect of fit
It is recommended that customers use a light interference fit between the inner ring and the shaft, and a transition or small clearance fit between the outer ring and the seat hole. Prevent the relative sliding between the shaft and the inner ring during the operation of the bearing, resulting in creep corrosion and abnormal temperature rise. At the same time, it can also avoid the reduction of the bearing axial capacity of the bearing side raceway during the creep process, and reduce the probability of premature failure of the cage caused by the irregular collision and extrusion of the steel ball and the cage, and at the same time reduce the risk of misalignment.
2. Reduce axial clearance
A small axial clearance is controlled to ensure that after the bearing is installed, a certain axial preload state is maintained between the two rows of raceways and the rolling elements, so as to avoid uneven loading of the two rows of raceways during operation. At the same time, the axial preload can also reduce the noise of the equipment, improve the rotation accuracy, and better meet the requirements of high-speed and low-noise equipment.
Customer benefits
Through the optimization of bearings and the adjustment of installation tolerance, the overall noise of the customer's equipment is reduced by 5 decibels during use, the running stability is greatly improved, and the power consumption is reduced by more than 20%. Maintenance costs reduced by 20%.